According to a study by the Fraunhofer Institute for Systems and Innovation Research [Fraunhofer ISI], battery production capacity in Europe alone will quadruple by 2025 from 124 gigawatt hours in 2022 to over 500 gigawatt hours. By 2030, this figure is expected to increase tenfold to up to 1.5 terawatt hours.
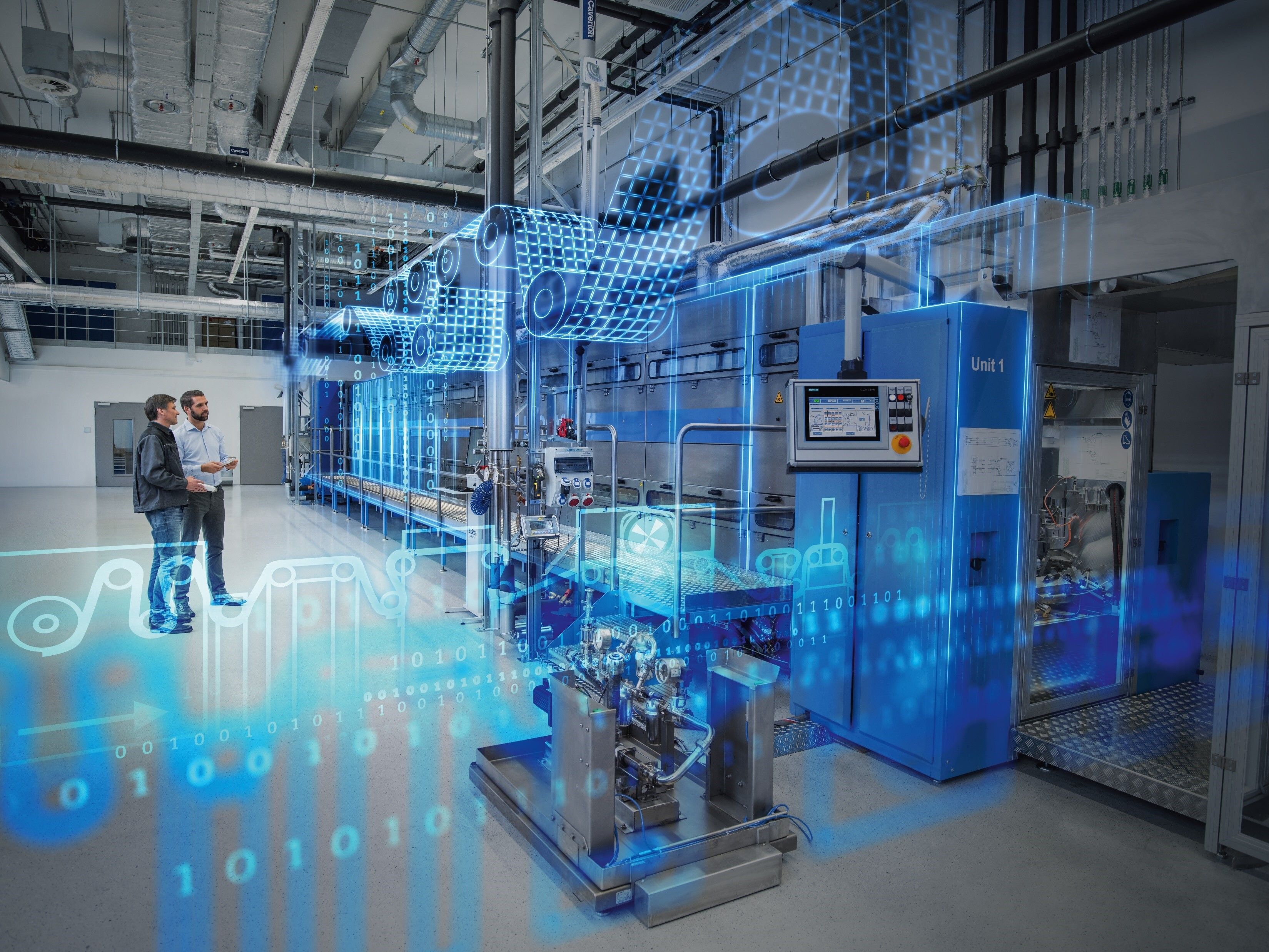
Given these projections, the largest German and Europe-wide unique competence center for developing and testing the production of battery cells – including for electrically powered vehicles – is currently being built in the Westphalian city of Münster. And a major milestone was just achieved in Münster on April 30, 2024: the commissioning of innovative European machine technology for the “FFB PreFab." This is an important step toward the establishing the "FFB Fab," which will enable industry-oriented production research on plant technology on an industrial scale in Münster.
As a battery cell factory focused on research and development, Fraunhofer FFB will make a key contribution to advancing the production of battery cells "Made in Germany" or "Made in Europe" and positioning them at the forefront of strong international competition.
To ensure that production in Germany can provide new battery technologies more efficiently, cost-effectively, and at the highest quality in the future, the Federal Ministry of Education and Research [BMBF] and the State of North Rhine-Westphalia are funding the creation of a facility for researching battery production with a total of up to €680 million as part of the "FoFeBat" project. Research production provides an infrastructure where small and medium-sized enterprises as well as large companies and research institutions can test, implement, and optimize the near-series production of new batteries.
The Fraunhofer-Gesellschaft is now implementing this project step by step with several partner companies.
One of these partners is Siemens AG, which is providing Fraunhofer FFB with software and hardware solutions based on the open Siemens Xcelerator platform. With their interoperable systems, the Digital Industries and Smart Infrastructure Business Units are contributing to the digitalization, automation, control, and monitoring of the machines, processes, and buildings. The real production and environmental conditions are being digitally mapped along the entire value chain by connecting OT [operational technology] to IT [information technology]. Sensors in the building and throughout the production environment will provide all relevant infrastructure data in real time.
Using the Manufacturing Execution System [MES] and the IIoT [Industrial Internet of Things] platform, Fraunhofer FFB will be able to plan, control, optimize, and flexibly scale its production processes. The Desigo CC building management platform will determine the optimal production environment with data-based and demand-oriented processes, even in clean-rooms and drying operations.
The collected data will be of central importance for Fraunhofer FFB in fulfilling its mission of researching the production of battery cells using a digital twin of the factory. The digital twin reflects the entire factory, from the technical building equipment to all production processes. This guarantees production under near-series and difficult conditions, e.g. clean room production, for a variety of industrial partners.
"Automation and digitalization are the keys to continuing to be competitive in industrial production in Germany in the future. With its construction of a new research factory for battery cells in Münster, the Fraunhofer-Gesellschaft will play an important pioneering role for the German electromobility supply industry. Siemens is contributing its industry-specific expertise in automation and digitalization," says Thorsten Selle, Head of the Siemens branch in Münster.
"Along with the Fraunhofer-Gesellschaft, we want to take the battery industry in Germany to the next level. When it comes to building automation and production equipment, we deliver innovative and sustainable solutions. With our expertise and decades of experience, we see ourselves as an integral part of the ecosystem of local value creation in electromobility," adds Markus Birkhan, Head of Vertical Battery at Siemens AG.