%20(3).png)
1. What are the major trends you’ve observed in the medical manufacturing and pharmaceutical industry over the past few years?
The past few years have seen radical changes in the medical and pharmaceutical industry. COVID-19 has accelerated the digital transformation, with organizations worldwide utilizing data to increase productivity and drive better patient outcomes. Similarly, healthcare providers are moving their practices and data management to online platforms, leveraging data to enhance diagnoses and patient treatment and improve customer experience.
The focus on data analytics is also fuelled by the demand to accelerate drug development and production. Aided by technologies such as predictive artificial intelligence (AI) and machine learning (ML) capabilities, additional insights can be gained on recommended next best actions. In the future, it is expected that the industry will place a much greater focus on data analytics, particularly on the ability to interact with data in real time.
We are also witnessing the general move towards smaller production and quantity of medical products. This comes as medications are becoming much more concentrated in each prescription, where each dosage is stronger and more potent. Moreover, the move towards small quantities in product manufacturing comes with increased demand for personalized products, due in part to the aging population and people’s enhanced awareness of their health and wellness.
To differentiate themselves from big pharma companies, some are opting to focus on new, precision-based medicines that may apply to smaller niches of the population and rare diseases. Personalized therapies maybe created based on genetic and biological characteristics of individual patients, and may even include social and environmental factors.
2. How has technology impacted the medical manufacturing and pharmaceutical industry during your time working in the sector?
We are seeing a demand for technology solutions that help rid the industry of its complexity — the processes within the manufacturingl and scape, the operations of physical plant equipment, and to make processes and workflows more turnkey in execution.
Technology is also helping to ensure that compliance and regulatory requirements are followed at all touchpoints across the value chain. Traditionally, the industry relied on indicators such as the number of recalls or OEE (Overall Equipment Effectiveness). These metrics were reported to institutional bodies on a fixed periodic basis to monitor trends and intervene in the manufacturing processes where necessary for the safety of the public.
Today, regulations are transitioning to a more holistic overview of the value chain. For instance, if a Contract Manufacturing Organization makes any changes, regulators desire the owner to be more compliant and immediately aware of the change. The extent of real-time data integration across the supply chain is something we have not seen in the past. Ultimately, regulators have been trying to push companies to be more data-aware, as technology and data quantify more elements of the process and potentially produce more quality metrics that are insightful by design.
3. What challenges do medical manufacturing and pharmaceutical companies face in terms of product development and bringing new products to market?
Even before the pandemic, launching a new pharmaceutical product was a massive and costly undertaking. Just steering the product through clinical trials was an impressive feat on its own, especially for first-time market entrants. In addition, companies would need to have a unique value proposition to stand out from their competitors.
This is especially so for personalized medicine, a field with very few industry experts. Companies often face challenges in finding the right personnel skilled for the job and turn to their ecosystem partners for each specific expertise. The depth of ecosystem collaboration means companies must be much more transparent to ensure quality control and compliance with regulatory requirements.
Additionally, supply chain disruptions became a major challenge for the global economy due to the pandemic. Multiple layers in the supply chain often involve several parties, making integration and communication difficult. Consequently, the industry experiences challenges in the quality distribution of biologicals, impacting the efficacy of the products delivered and raising health concerns for end consumers.
Moreover, the industry needs to abide by strict international regulations regarding trade, public health, product safety, and industry standards. Pharmaceuticals are one of the most sensitive goods in transport as their viability can be compromised by a myriad of factors, including storage conditions. The contamination of pharmaceuticals poses signficant dangers and could reduce the drug’s efficacy. As such,organizations will need to leverage end-to-end monitoring tools to minimize hindrance to product development and roll out.
4. What strategies do medical manufacturing and pharmaceutical companies use to ensure quality control and compliance with regulatory requirements?
Medical and pharmaceutical companies use a range of strategies to ensure quality control and compliance. Some of these include:
· Establishing quality management systems that meet the regulatory requirements across territories. This includes outlining the procedures and processes that ensure products are manufactured to meet predetermined specifications and are safe and effective for their intended use.
· Conducting regular audits of existing systems and processes to ensure companies comply with regulatory requirements. This includes documenting the manufacturing processes, as well as testing and quality control processes. Companies can also monitor the results of the audits and testing, and implement corrective actions when necessary.
· Conducting extensive product testing to ensure that all products meet the required safety and quality standards. This includes the testing or analysis of all materials, processes, equipment,techniques, environments and providing staff training to ensure their final products are consistent, safe, and effective. This is necessary to prevent product adulteration and microbial contamination, as public health and safety is at stake.
5. What roles do software and data analytics play in the medical manufacturing and pharmaceutical industry, and how have you seen this evolve over time?
The current industry buzzword is plug-and-play compatibility. The evolution in the pharmaceutical industry has seen a bigger desire for off-the-shelf software and data products by vendors – and this is where software and data analytics come into play. With the right software, businesses can now spend less time designing the data repository architectures,less troubleshooting the workflows that feed into their systems for regulatory compliance, and better connectivity of plant equipment across different manufacturers.
The big challenge that remains is getting all sources of data — from sophisticated batch-oriented results, ERP (Enterprise Resource Planning) systems, MES (Manufacturing Execution Systems) — together into a single location to be mined effectively. Through the deployment of a digital manufacturing operations management system, pharmaceutical manufacturers may achieve more accountability during their periodic review – where the business reviews the quality metrics and parameters in product manufacturing.
The other evolution is the rise of multi-variate process control, particularly in biologics therapy. Pharmaceutical manufacturers are trying to build a model to predict the quality of a batch. Through a predictive advanced process control system, manufacturers can assess the viability of an eight-week batch on the third day of testing. This eliminates significant time and allows the chance to restart if required. Companies may apply data in ways that improve their processes and reduces their time-to-market for products.
6. How are companies utilizing new technologies in medical manufacturing and pharmaceuticals?
Time-to-market is an essential concept in the medical industry. It takes 10 to 12 years to get a product on the market, and only 1 in 100 drugs will make it through that process. In addition, each drug has about 7,000 parameters that need to be tracked throughout the production lifecycle to adhere to stringent regulatory requirements.
That is at the heart of the data challenge. Companies desire to have a more comprehensive way to review, track and analyze their data. However, the reality is that it is not as easy or as simple as it looks to aggregate data in a cleaner way when companies need to operate with multiple equipment vendors. There is not a standardized data structure, and it is not easy to aggregate data in a consistent way from an analysis perspective.
This is where new technologies in data analytics may help overcome the challenge. For example, Biogen wanted to manufacture enough Aducanumab to treat one million Alzheimer’s patients worldwide. However, that required increasing production, improving yield, and reducing costs. The company used AVEVA PISystem to enable real-time visibility and contextualized insights on the plant floor. With over 15 years of expertise and industry wisdom to get the AVEVA PIsystem recognised as the de-facto platform and standard in the industrial intelligence space, Biogen can now make adjustments before the batch moves onto the next step, allowing the company to reduce costs, increase yield, and expand production efforts.
The future of medical manufacturing will always be more data-driven, and what we can do, is find better ways of harmonizing technology that enables businesses and industries to do what they do best.
Find out more at https://www.aveva.com/en/
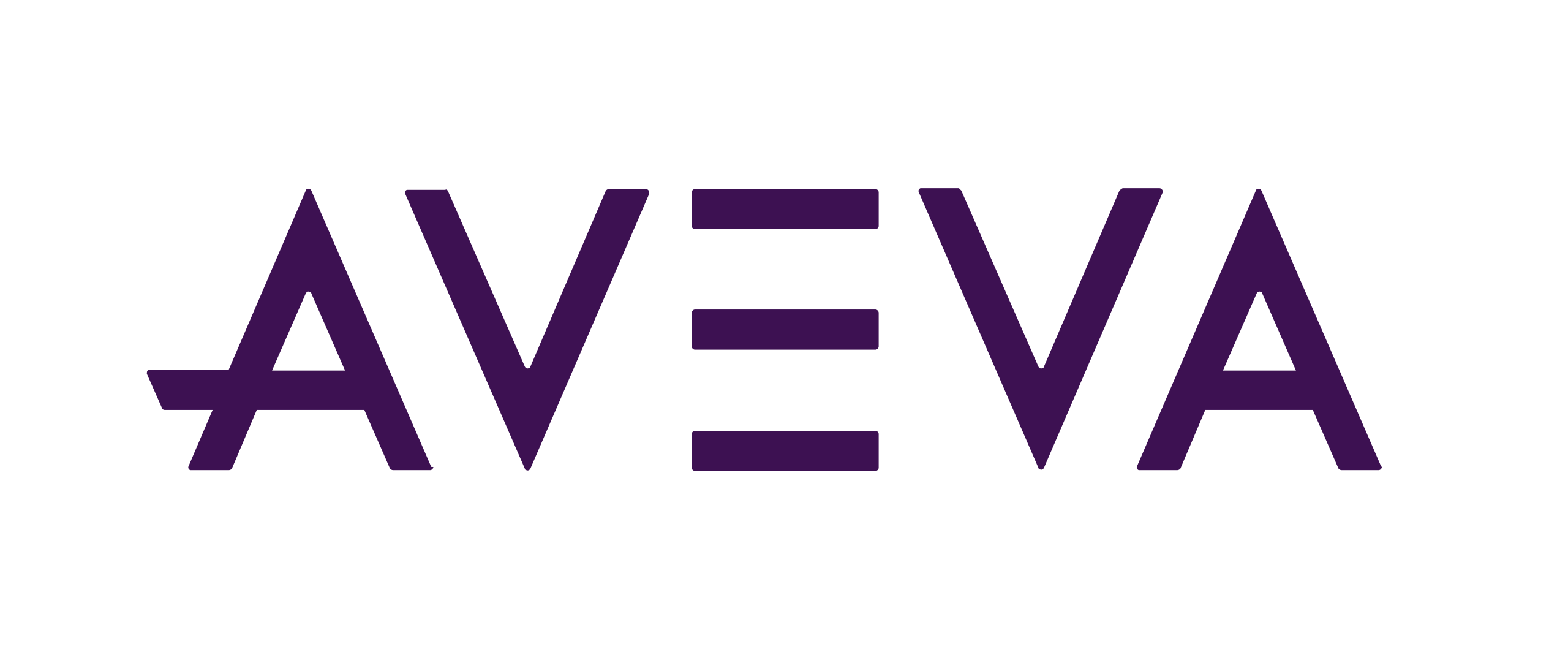