Completely Renewed
STUDER cylindrical grinding machines – many years of high performance and preci-sion. A machine overhaul by STUDER breathes new life into an old cylindrical grinding machine and provides the same precision as the day it was delivered. There are also numerous options available for expanding and modernizing machines.
Whether in small series or high-volume production: If cylindrical grinding machines have per-formed at a high level for many years, their precision will eventually, at some point, deteriorate. With intensive machine use or when working with aggressive materials or certain cooling lubricants, this is often the case even sooner. Thankfully, a comprehensive overhaul can breathe new life into an old machine and restore it to the same condition as the day it arrived.
A machine overhaul can be a worthwhile option, especially if a company intends to grind the same workpieces as before and does not necessarily want a technological upgrade. "The cost is around 50 to 60 percent of the purchase price of a new machine," explains Marcos Cotarelo, Head of Customer Care Sales at Fritz Studer AG. In addition to the complete overhaul of all sub-assemblies, STUDER is the only machine manufacturer to completely replace and renew the guide ways according to original specifications with the Granitan® S200 guideway coating. Consequently, the geometry after installation of the sub-assemblies will correspond to that of a new machine and offer the same precision and accuracy as when it was first delivered.
Transforming Old to New
A complete overhaul involves much more than just a simple repair. The machine is taken to the plant in the Swiss town of Thun, where it is disassembled completely for a thorough inspection. By using original parts combined with the expert knowledge of STUDER employees, sustainable quality and maximum precision can be guaranteed once again. And that's not all – revision of components by the OEM (Original Equipment Manufacturer), cleaning of the enclosure by sandblasting, a new coat of paint, perhaps even with special coatings, and the replacement of wear parts – all of this, and more, helps to ensure that even a 20-year-old machine can work and look like new again. Customers are often surprised and delighted by this transformation as they now have an as-new machine again, with a great price-performance ratio. In addition to overhauling the entire machine, overhauling individual sub-assemblies, such as the workhead, wheel head, and tailstock, is also an option.
A major benefit of a global company like STUDER is its many years of experience and expertise at an international level. After all, delivery and return transport of a - grinding machine weighing several tons, as well as managing the necessary permits and customs formalities is no mean feat. As a STUDER customer, you can be confident that wherever you are in the world, once you have contacted us, a Customer Care Consultant will visit your premises to provide individual advice based on your requests and requirements. If, once you've considered the relevant factors, you decide that a machine overhaul is what you need, our overhaul team will get to work.
A team of more than 25 employees takes care of various machine and sub-assembly over-hauls each year. In addition, specialists from the new machine production, electronics or mechanics, as well as import-export, logistics, and customs ensure that everything runs seamlessly, whether in Europe or elsewhere in the world. They help to keep the complex logistics and technical processes of a machine overhaul as simple as possible. This includes delivery and return shipment, as well as commissioning of the overhauled machines. Before shipment, all machines undergo a function and geometry test in the manufacturer's plant and are issued with a new original manufacturer certificate.
Trusted Machines With new Capabilities
After a machine overhaul, companies can enjoy a one-year warranty and support from an outstanding technical service team. It takes STUDER an average of 12 to 14 weeks to complete a full overhaul. During the overhaul, companies can take advantage of a machine on loan to prevent production standstills. It is not uncommon in the course of an overhaul, that customers opt for a modernization or expansion of the range of parts that they would like to manufacture. This could mean retrofitting a measuring head, an additional internal grinding spindle, new spindle cooling, a hydraulically swiveling dressing unit, or a new workhead– there are countless options available. Importantly though, a machine overhaul can bring new capabilities to a trusted system.
A significant improvement in production efficiency can be achieved with a subsequent automa-tion solution if desired. This would allow a supposedly “old” machine to process workpieces independently and automatically, giving employees the flexibility to spend time on other tasks once the loader has been replenished. In addition, a software update can facilitate assistance systems for monitoring or maintenance purposes. Despite the additional features and the as-new look that a machine overhaul can bring, the machine remains the same machine that users will be familiar with. That means not having to relearn something that they already know. Along with the efficiency that an overhaul adds, this is an important point that makes it appealing to so many companies. They can continue using a familiar machine long into the future, as it will now have the same service life as a new system.
A machineoverhaul at a glance
- Machine bed: completely overhauled, the knobbed pattern is milled off, the guide ways recast, and the base repainted.
- El. Enclosure: replacement of the wear parts in the electrical cabinet
- Pneumatics: new valves, hoses, and filters.
- Hydraulics: new hydraulic and lubrication system, all valves and hoses are replaced.
- Workhead: completely overhauled.
- Wheelhead: completely overhauled.
- Tailstock: completely overhauled.
- Axes: table as good as new,installation of a new recirculating ball screw and bearings.
- Machine enclosure: sandblasted, new topcoat, color according to STUDER design or customer preferences.
- Control system: existing controller retained.
- Delivery: always with careful measurement of the geometrical tolerances of the new machine, including test protocols.
- Loan machine: we can provide a loan machine on request.
- New original CE certificate
- Automation solutions on request
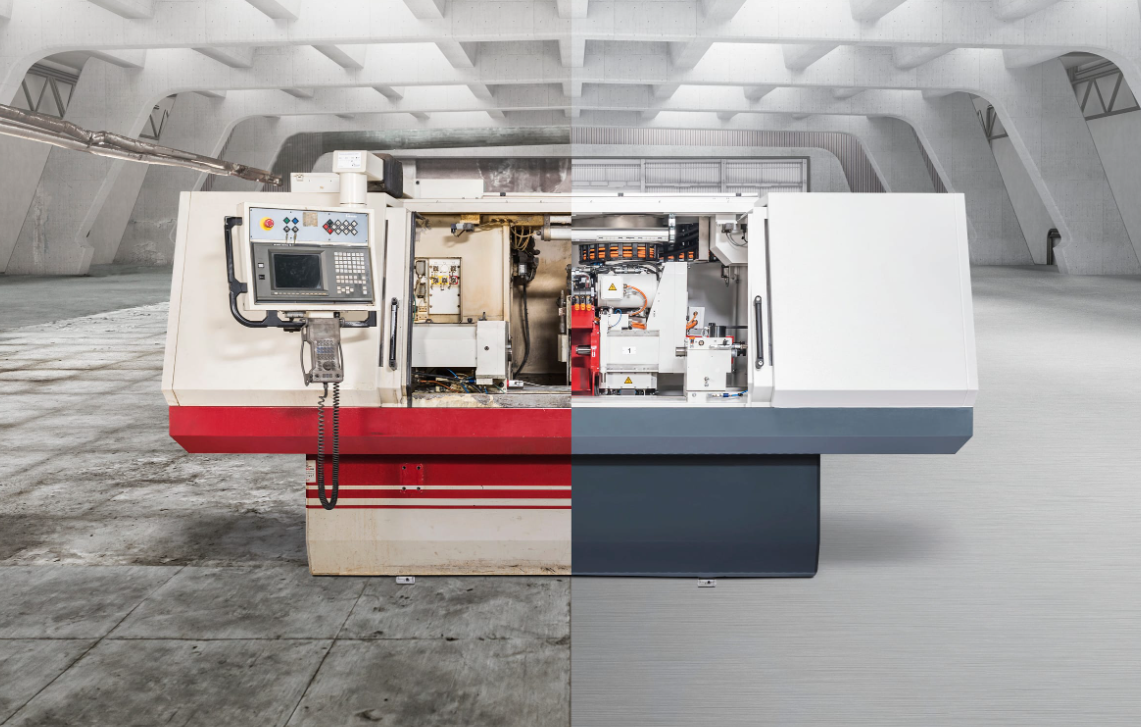
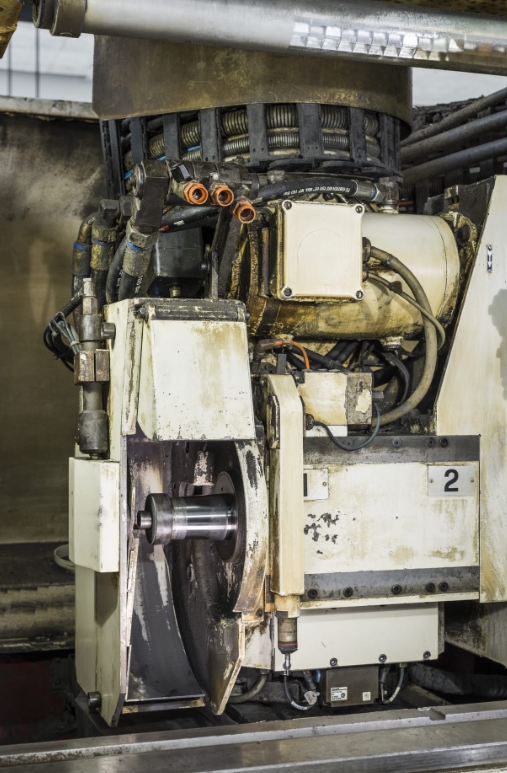
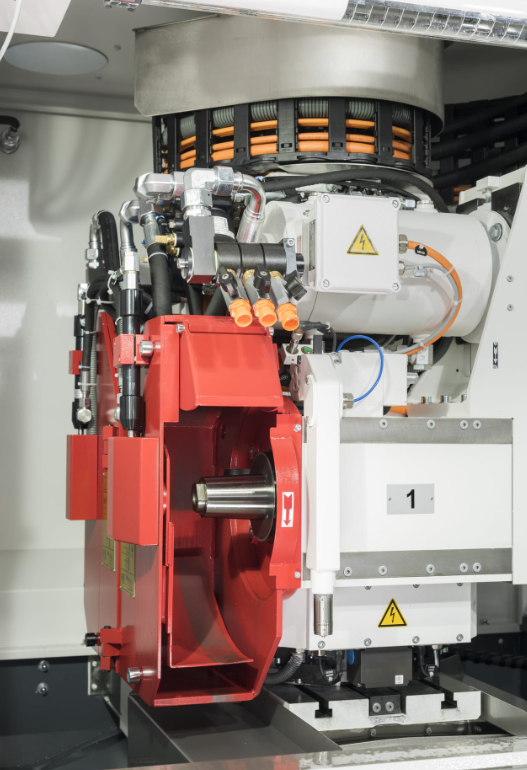