%20(4).png)
1. What is the challenge posed by Industry 4.0, particularly in terms of automated production and workforce reduction?
The challenge posed by Industry 4.0, particularly in terms of automated production and workforce reduction, revolves around the rapid and profound shift towards automation. While the goal is to create highly interconnected and efficient production processes, this often means that routine and labor-intensive tasks are being taken over by machines and intelligent systems, potentially leading to a reduced need for manual labor. Machines, equipped with sensors and artificial intelligence, are increasingly capable of performing complex tasks that were once the domain of human workers. This transformation necessitates careful consideration of workforce management, including reskilling and upskilling programs to ensure that the workforce remains adaptable and competitive in this evolving landscape. Additionally, the challenge lies in striking the right balance between automation and human involvement, emphasizing human-machine collaboration and the utilization of human skills in tasks that require creativity, problem-solving, and decision-making.
2. Can you elaborate on the processes involved in digitization and automation within Industry 4.0?
Certainly, Industry 4.0 introduces a comprehensive transformation through digitization and automation. Firstly, automating machine operations involves equipping machinery with sensors and connectivity, allowing them to communicate and adapt in real-time, optimizing production efficiency and enabling predictive maintenance. Secondly, material transportation is streamlined with autonomous guided vehicles (AGVs), conveyor systems, and IoT, reducing manual labor and enhancing logistics precision. Thirdly, quality measurement devices, like machine vision systems and sensors, ensure consistent and precise product inspection. Lastly, data analysis plays a central role, optimizing energy management by harnessing data to monitor and control energy usage, contributing to sustainability and cost-efficiency. Together, these processes redefine industrial processes, making them more efficient, flexible, and data-driven.
3. What role does data usage play in the processes of Industry 4.0?
Data usage plays a central and transformative role in Industry 4.0 processes. It serves as the lifeblood of this industrial revolution, influencing the effectiveness and efficiency of various aspects throughout the manufacturing and industrial landscape. At its core, Industry 4.0 leverages data from a multitude of sources, such as sensors, IoT devices, and interconnected machines, to enable real-time monitoring and decision-making. This data is processed and analyzed through advanced analytics, machine learning, and artificial intelligence, allowing for production optimization by identifying inefficiencies and enabling just-in-time manufacturing. Moreover, predictive maintenance is made possible, as data-driven insights can forecast when machinery requires attention, minimizing downtime and reducing costs. Data usage in Industry 4.0 extends beyond the shop floor; it empowers supply chain management, quality control, and energy efficiency, ultimately fostering a more agile, competitive, and responsive industrial ecosystem.
4. Could you shed light on the concept of Industry 5.0 and its relation to human-machine collaboration?
Embarking on the grand stage of Industrial 5.0, we delve into its unique melody, poised to differentiate itself from the echoes of past Industrial Revolutions. Personally, I've often found discussions about the Industrial Revolution to be a complex cadence. Amidst this symphony, harmonious collaborations take root, exemplified by the cohort for optics gracefully supporting human artisans in realms such as assembly and welding. This dynamic interplay promises to endure and flourish. As we navigate the choreography of integration, envisioning its seamless fusion within processes and across diverse production lines beckons our attention. As of now, the label "revolution" seems less apt, given the familiarity of robots in our narrative over time. The major players in robotics - Arno, KUKA, ABB, and Universal Robots - have sculpted the landscape with their innovative contributions. A fresh dimension emerges today, as IGUS, a company synonymous with plastic parts, diversifies its repertoire, crafting components for machinery from this versatile material. The transformation in their business model also extends to cobots, redefining the tempo of evolution. In this symphony, a cobot, akin to a vigilant guardian, employs sensors to halt its actions upon contact with any element. As the narrative unfolds, Industrial 5.0 showcases a harmonic convergence of humans, machinery, and innovation, truly redefining the opera of progress.
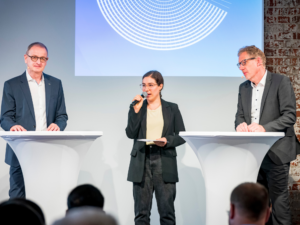
5. How does artificial intelligence (AI) factor into Industry 4.0?
Certainly, the realm of artificial intelligence encompasses a vast expanse, with significant implications spanning from consumer products to the likes of Chet Chibiti and various other applications. It's crucial to recognize that we're essentially orchestrating a process, one that demands a coherent introduction and yields a discernible output. Thus, establishing a profound correlation between input data and resultant effects becomes an indispensable facet.
Moreover, the deployment of artificial intelligence comes to the fore when dealing with copious amounts of data derived from processes or machinery. This reservoir of information lends itself to intricate analysis, unraveling the nuances of occurrences. Nonetheless, the incorporation of these analytical outcomes back into the machinery poses challenges. A paramount concern revolves around the assurance of safety - a priority upheld particularly in European regions due to the machinery directive. This imperative mandates the perpetual guarantee of the machine's safety, ensuring that humans remain unscathed by its operations.
6. What are some of the challenges faced by the German machine tool industry, and how are they being addressed?
The German machine tool industry, renowned for its precision engineering and global leadership, indeed faces various challenges. One of the prominent issues is the recent economic turbulence, including supply chain disruptions and material shortages triggered by global events such as the COVID-19 pandemic. To address these challenges, the industry is focusing on several strategies. First, there is an emphasis on managing demand fluctuations through agile production techniques, allowing manufacturers to quickly adapt to changing market conditions. Second, there's a concerted effort to enhance supply chain resilience by diversifying suppliers and adopting digital technologies for real-time visibility into the supply chain. Additionally, the German machine tool industry is actively engaging with international investment programs and partnerships to secure access to critical materials and strengthen its global competitiveness. By adopting these measures, the industry aims to navigate through these challenging times and maintain its position as a global leader in precision machinery.
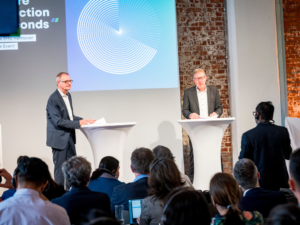
7. What opportunities and challenges do you anticipate for the German machine tool industry in the future?
In the future, the German machine tool industry will encounter a dynamic landscape with both opportunities and challenges. On the opportunity side, embracing emerging technologies like Industry 4.0, artificial intelligence, and automation can open up new avenues for innovation and efficiency, enabling the industry to meet evolving customer demands effectively. However, these opportunities come with their own set of challenges. Staying innovative and at the forefront of technological advancements is paramount to remain competitive in a rapidly evolving market. Moreover, addressing sustainability concerns by adopting eco-friendly manufacturing practices and materials will be essential, as environmental regulations and customer preferences increasingly prioritize sustainability. Additionally, ensuring a skilled and adaptable workforce will be critical for the industry's growth, as it navigates the complexities of advanced technologies. Successfully balancing these challenges and opportunities will be crucial for the German machine tool industry's continued success on the global stage.
8. With new trends and technological advancement, do you think you have a notable impact on the future of the German machine tool industry?
It will continue to revolve around digitization, as I mentioned earlier. Currently, and as discussed with our members, the challenge lies in the absence of sufficient standardization. Not all small and medium-sized companies can explore new functions or develop new functionalities from data, for instance. This is partly due to European regulations. Additionally, the topic of sustainability poses a challenge. Moreover, there is a shortage of workforce. This isn't solely restricted to IT specialists, even though they are crucial in the context of Industry 4.0. However, there's still a shortage. A highly educated workforce is essential on the shop floor, managing operations, and handling intricate assembly processes. Unfortunately, these skilled individuals are also lacking. Without them, it's impossible to scale up production. The shortage of skilled workers is a significant concern.
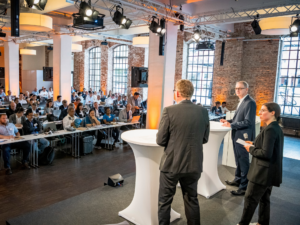
9. What do you predict will be the main opportunities and challenges for the German machine tool industry? What approaches should companies in this sector employ to guarantee enduring expansion and achievement?
Navigating tough international competition and fostering innovation across all product sectors remains an ongoing challenge. This competitive landscape has been evident over the past years, as industries in Europe—such as Switzerland and Italy—and also in Asia, including Japan and Korea, continuously develop new products. In this context, maintaining a competitive edge is essential. Embracing new technologies in materials, sensors, automation, and digitization is crucial, given that a machine is an amalgamation of diverse technologies. This calls for the ability to analyze the next steps of innovation that cater to customer demands. While impressive machines might exist, their success depends on aligning with customer needs. This skill is a distinctive strength among German and European producers, who excel at understanding customer requirements and delivering tailored solutions. Staying ahead in this regard holds paramount importance.
10. Today I just checked that about 54 Korean companies are planning to participate in the show. And also DN Solutions also gave a short presentation. But from your perspective, how do you see the Korean market?
From my perspective, the Korean market presents itself with dual facets that warrant consideration. While the precise number of Korean manufacturing companies isn't the sole defining factor, it's important to note that the presence of companies from other regions, such as Japan, China, and Taiwan, also contributes to the landscape. Within Korea, there are notably well-established and adept companies spanning various technological domains. Their reputation extends internationally, as evidenced by their growing exports and solid standing in the global market.
In terms of supply, Korea emerges as a robust contributor to the machine tools sector. The nation boasts a strong presence in supplying cutting-edge machinery. On the demand side, Korea aligns with other prominent industrial nations like Europe and Japan. The country's industries, including electronics, automotive manufacturing, shipbuilding, and more, collectively drive its economy. The harmonious balance between demand, production, and supply facilitates consistent and vigorous growth. This dynamic contributes to Korea's status as a thriving developing nation in terms of both market and industrial production. Consequently, the nation becomes a favorable destination for companies in Germany seeking export opportunities. The symbiotic relationship between Korea's industriousness and Germany's prowess makes for a mutually beneficial trade partnership.
Visit EMO Hannover this sept https://emo-hannover.de/en
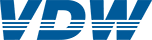