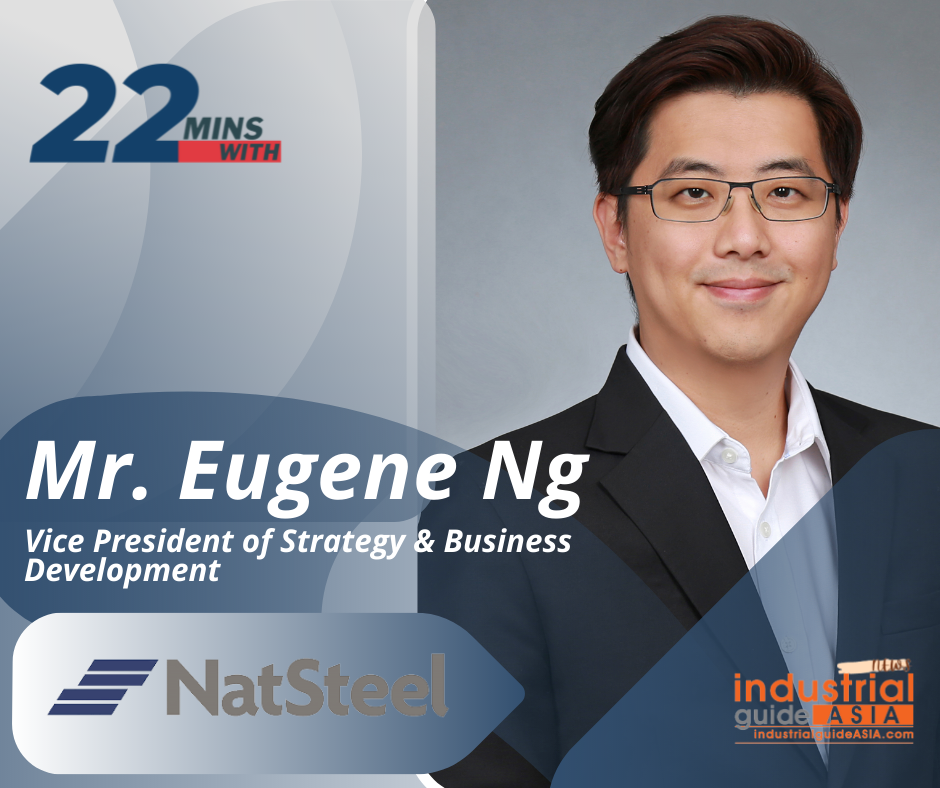
Mr. Eugene Ng Peng Guan - Vice President of Strategy and Business Development
1) What are some of the most important factors to consider when formulating a sustainability plan?
When formulating a sustainability plan, businesses should first understand their footprint. Only after grasping their environmental impact, can companies understand what changes need to be made. With better knowledge of which parts of their value chain contribute the most significantly to carbon emissions, companies can set realistic, achievable targets in these areas.
Another important factor to consider when formulating a sustainability plan is the need to account for the long run and potential changes in industry circumstances. Companies have to understand that changes and developments in the industry may occur along the way, as such there is a need for the sustainability plan to account for this.
2) What would your approach be to helping NatSteel navigate these considerations?
In all that we do, NatSteel strives to be a company that is forward-thinking and we are constantly looking for new ways to improve the sustainability and eco-friendliness of our processes. NatSteel keeps abreast of developments in the industry, and we are kept up to date of upcoming technologies which we can implement in our practices. With all these in mind, we can be sure that any sustainability plans that we formulate are for the long-term and can be carried out realistically.
3) What do you think is the biggest barrier to achieving a sustainable future?
Globally, steel is inextricably linked with economic growth and prosperity and it has enabled our modern way of living. However at the same time, the steel industry has a huge environmental impact, in terms of carbon emissions and the amount of resources steel production takes up. Steel production requires the utilisation of a large amount of energy and water.
However, the extent of environmental impact depends greatly on the type of technology used in steel production, and this technology has improved throughout the years. We have been using an electric arc furnace which is more environmentally-friendly compared to blast furnace technology.
4) What is Natsteel doing to reduce the environmental impact of its manufacturing process?
As part of NatSteel’s culture, we have been driving energy-saving project initiatives. With our electric arc furnace technology, scrap is first heated before being lowered into the furnace. This cuts the power use in steel production by a significant amount.
NatSteel also endorses the use of green steel, by using recycled metal scrap to produce steel. Singapore generates 1.2mil MT of scrap a year. NatSteel collects these scraps from all parts of Singapore, and we process them through our furnaces to produce steel. The steel that is produced goes back into much of the infrastructure that is built in Singapore, such as HDBs, condominiums, highways and MRTs, hence in a sense it is a cyclical economy because of our practices.
We also recently introduced a stronger type of steel to be used in construction, which is Grade 600. By using a stronger type of steel, this means construction projects will be using less steel which translates to lower emission and resource required during the manufacturing process.
5) What are the advantages of using Grade 600 materials in Singapore's current infrastructure?
Grade 600 is a high strength reinforcement steel, already approved by BCA, and used in Singapore for the construction of Residential, Commercial, Industrial and Infrastructure projects. With its 20% superior yield strength over the commonly used Grade 500 steel, Grade 600 is gaining traction in Singapore’s construction industry today.
For construction projects, this means potential steel savings of up to 20% and ease of rebar congestion which improves construction quality. This also means Shorter reinforcement fixing time and reduced manpower required on site for steel fixing.
For developers, stronger steel translates to thinner walls, columns and beams. This means we can have more usable spaces within buildings. Especially since Singapore is such a small country with relatively less land space for buildings, it is important that we maximise the use of the land space we have.
A few projects using Grade 600 are Kim Chuan Depot Extension, Jurong Port Ready-Mixed Concrete Port-Centric Ecosystem, One Pearl Bank, Jurong Innovation District and Punggol Digital District.
6) What have been the key challenges for NatSteel in recent years?
NatSteel is also constantly looking for how else we can save power and energy, and how we can run more efficiently. Using our electric arc furnaces as an example, one of the main resources that we need is electricity. At the same time, the cost of electricity is much higher in Singapore than in most other parts of the world. Yet, we have to be competitive against other steel mills, hence this has become one of the driving forces for us to find ways on how we can make steel in a cleaner and cheaper way.
Another challenge is getting customers to make the switch to Grade 600 and cleaner materials. With most of the construction that happens in Singapore, there lacks a significant differentiation between the use of green steel and other conventional steel. We have been trying to increase the demand for green steel and shift our customers towards its use, and are still currently in the midst of doing so.
7) How will Natsteel maintain its competitiveness despite being the only steel mill in Singapore and that to say facing a very strong competition in this region?
In Singapore, NatSteel is focusing more on value-add services, in line with the Government’s push for integrated digital delivery in the construction sector.
The Building Information Modelling (BIM), is a technology that improves productivity and integration across various stakeholders along the entire construction value chain. Our BIM specialists collaborate closely with stakeholders to produce BIM rebar requirements in a 3D model of the construction project. With accurate reinforcement information, this will improve the cycle time in the planning process and reduce errors.
We also rolled out NiCE(NatSteel Integrated Customer Experience), a portal for our customers to make orders, view real-time delivery schedule and a cloud-based document portal, similar to any internet banking portal you use today. This digital transformation allows customers to cut back on paper usage, get real time information, access to digital documents and helps to push Singapore towards being a more sustainable construction space.
8) How do you intend to expand your company's customer base internationally?
At the moment, NatSteel has an established presence across Southeast Asia, with facilities in Singapore, Malaysia and Thailand. We are looking to strengthen our presence in each of these countries first, before expanding into other countries. This will be done by improving and upgrading our facility production capacities and further streamlining our processes to make our steel production process cheaper and more efficient. We are also hoping to lead the industry in making the switch towards more environmentally-friendly processes, first within the region and then worldwide.
9) What do you hope will be different about the heavy machinery industry in the future?
Many believe that it is difficult for the steel industry to achieve sustainability, due to the nature of the industry (steel production greatly contributes to carbon dioxide greenhouse gas emissions). In Singapore, the steel industry has a carbon footprint of about 52 million tonnes a year. However, despite being a leading Southeast Asian steel company, NatSteel only contributes to 0.3% of this carbon footprint.
NatSteel is leading the industry in terms of sustainability, as we operate one of the most energy efficient electric arc furnaces in the world. NatSteel utilises 30% less energy to produce a tonne of steel, compared to other electric arc furnace operations. This is achieved by adopting various technologies such as electric arc furnaces to reduce overall energy consumption, and the use of virtual lance burners, among many other technologies.
We hope that other players in the heavy machinery industry will similarly make the switch towards more energy-friendly and sustainable practices, in order to minimise the carbon footprint this industry has as a whole. At the current moment, about 70% steel made comes from the blast furnace route, and the remaining 30% comes from the more environmentally-friendly electric arc furnace route. Thankfully, with the way the industry is developing, we expect electric arc furnace technology to pick up and replace the blast furnace route, and we can also expect the development and utilisation of newer, cleaner technologies within the next five to ten years.
10) What are some of the challenges facing the manufacturing and construction industry in Singapore? How do you think NatSteel can close this gap?
The construction sector has been badly hit by the COVID-19 pandemic, and one of the current main challenges is the shortage of manpower. What NatSteel is doing at the moment to close this gap is increasing automation and digitalisation of our products and services, so that there is reduced reliance on manpower and foreign labour. By making the shift towards automation, this also improves workplace safety by minimising any potential for workplace accidents.
For more information please visit https://www.natsteel.com.sg/
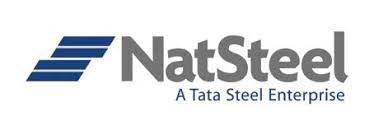