The Spanish TEMSA Metallurgical Group is one of the world's leading manufacturers of special tools for cold forming. The company has also been using cylindrical grind-ing machines from STUDER in its production for many years. A visit to the TEMSA plant in Barcelona.
Wearing a white work shirt, Alfonso Vivar walks through a large hall that radiates a sense of order, despite its multitude of machinery, workstations with monitors, and focused employees. Everything has its place, every work step is carefully planned, and at its heart is a yellow robot arm working away methodically. We are located in an 8,000 square meter (86`000 sq. ft) high-tech plant to the west of Barcelona, Spain. Production Manager Alfonso Vivar knows every corner of the plant. His shirt bears the bright red logo of his employer, TEMSA Metallurgical Group, a leading global specialist in the production of high-precision tools for cold forming and an ex-pert in powder metallurgy, sintering, and fine cutting.
With cold forming, metal below the recrystallization temperature is forced into a specific shape using high compressive and tensile forces. Compared to metal-cutting operations, this allows for shorter processing times per workpiece, thereby reducing costs in series production. Cold forming also allows for high strength, complex ge-ometries, and excellent surface properties. Components produced using this method include those for high-tech industries such as aerospace and automotive. All of which this can only be accomplished with the right special-purpose tools and skills, which is exactly where TEMSA comes into play.
"Our team can manufacture special tools in a tolerance range of just a mikron (0.000,040”)," explains Vivar, proudly. TEMSA's site in Barcelona has around one hundred employees, all working to manufacture tools to exacting customer requirements. "Our expertise also helps us to accomplish short lead times. But that's only because we use the very best machinery," he concludes.
Confidence in the Technology
"This is our new STUDER S100, which we acquired earlier this year, together with a favoritCNC." Vivar points to the CNC universal internal cylindrical grinding machine, painted white with blue accents. This color combination is typical of STUDER's cylindrical grinding machines and is a familiar sight at the TEMSA plant – the company has been using the Swiss manufacturer's machinery in its production facilities for many years. The company operates several STUDER machines for grinding tasks, including the S131, a new-generation CNC universal machine for internal cylindrical grinding. "We have confidence in the technology and value the positive relationship we have with the manufacturer," explains Vivar of the decision to invest. In addition, the high level of precision, reliability, and ease of operation offered by STUDER ma-chinery machines help to ensure that production is as efficient as it can be.
As an example, the S100 is a great all-rounder offering maximum precision thanks to its numerous options for internal, face, and external grinding. The machine facilitates the production of a wide range of workpieces up to 550 mm (21.65 “) in length. The favoritCNC is a CNC universal cylindrical grinding machine for individual and batch production of medium-sized workpieces with a length of up to 680 mm (26.8”). Both machines have an exceptional price-performance ratio, while at the same time offer-ing premium technology, such as the machine bed of solid mineral cast Granitan® and optimal hardware-software interplay for ease of operation. The S131 for internal cylindrical grinding with patented StuderGuide® guide system, turret wheelhead with up to four grinding spindles, and an additional C-axis is ideal for high-precision manufacture of flanged parts and smaller workpieces in a wide range of applications.
Customer Service with Direct Communication
In addition to the quality level of the machinery, Vivar cites another important reason for opting for STUDER – "The customer service is outstanding, and we have several contact persons who can speak Spanish," he explains. This helps to ensure easy and direct communication. He also values what STUDER has to offer in terms of preven-tive maintenance. This includes regular and routine inspections of the machinery by STUDER's technical personnel, designed to minimize the risk of production failures and improve their operational durability.
Standing next to Alfonso Vivar is Riccardo Delai, Sales Manager for Latin Europe at STUDER. He visits the plant in Barcelona at regular intervals and is often on the phone with TEMSA employees. "The personal contact is extremely important as it helps me to know what is working well and what needs attention," he explains. STU-DER has recently appointed a local service technician for Spain, allowing a faster response to customer inquiries. Delai considers the southern European country an important market for future growth, not least because of the Spanish government's support, along with that of the European Union, for local companies with investments in high technology. "We are delighted with the international success of TEMSA as a fully Spanish company, and it clearly demonstrates what can be achieved with our machinery," emphasizes Delai.
Investing in the Future Safeguards Success
TEMSA's success story goes back more than 30 years when the fledgling company produced high-precision tools from tungsten carbide and steel. Through consistent investment in employees, expertise, and state-of-the-art systems, the Spanish com-pany has quickly been able to establish an excellent reputation around the world. To-day, the company is a world leader in special tools for cold-forming processes. "I am extremely proud of our team; we are one big family. We have many second-generation employees working with us, and at Christmas, we always have a meal together with the first generation," explains Vivar, a TEMSA veteran of 25 years.
This appreciation for tradition is paired with foresight for the future, and TEMSA was an early adopter of automation as a means to make production more efficient. One such example is the yellow, 360-degree operating robot arm here in the plant, which automatically sorts numerous tools and allocates them to the machine according to requirements and processing cycles. "We want to move automation up a level in the future, which is a real challenge," explains Vivar. This is another area in which STU-DER is a valuable partner, having ample experience in customized and standardized automation solutions. As an example, the S100 can be equipped with a loader inter-face and automatic sliding door and thus integrated into an automated production line. The S131 also has a standardized interface for a loader and peripheral equipment.
Alfonso Vivar and Riccardo Delai continue their tour of the large TEMSA hall, passing robot arms, machinery, and focused employees. "I am delighted that TEMSA is hap-py with its two new STUDER machines", says Delai and shakes Vivar's hand to say goodbye. "And me too," laughs the Production Manager, adding "See you next time".
Just one example of this is the yellow, 360-degree operating robot arm here in the factory, which automatically sorts a large number of tools and allocates them to the machine depending on the processing cycle.
The S100 at a Glance:
• Tried-and-tested CNC universal machine for internal cylindrical grinding with high precision and excellent price-to-performance ratio
• Workpiece length incl. clamping device max. 550 mm (21.65 “) and workpiece diameter max. 420 mm (16.5”)
• Straightforward operation and programming support thanks to StuderPictogram-ming, short setup and retooling times with STUDER QuickSet, and automatic grinding spindle revolver
The favoritCNC at a Glance:
• CNC universal cylindrical grinding machine for medium-sized workpieces in one-off and series production (max. 80/120 kg (176/264 lbs)) with excellent price-to-performance ratio
• External and internal grinding possible in one setup
• Straightforward programming with StuderPictogramming and optional Studer-GRIND for the creation of grinding and dressing programs on an external PC
The S131 at a Glance:
• Latest-generation CNC universal machine for internal cylindrical grinding for workpiece lengths of 300 mm (11.8”) (incl. clamping device) and a workpiece di-ameter of 250 mm (9.85”) (max. 100 kg/220 lbs)
• StuderGuide® guide system with linear drive and grinding spindle revolver with up to four grinding spindles
• C-axis for workhead for form and thread grinding
• Standardized interface for loader and peripheral equipment and automatically swiveling workpiece table
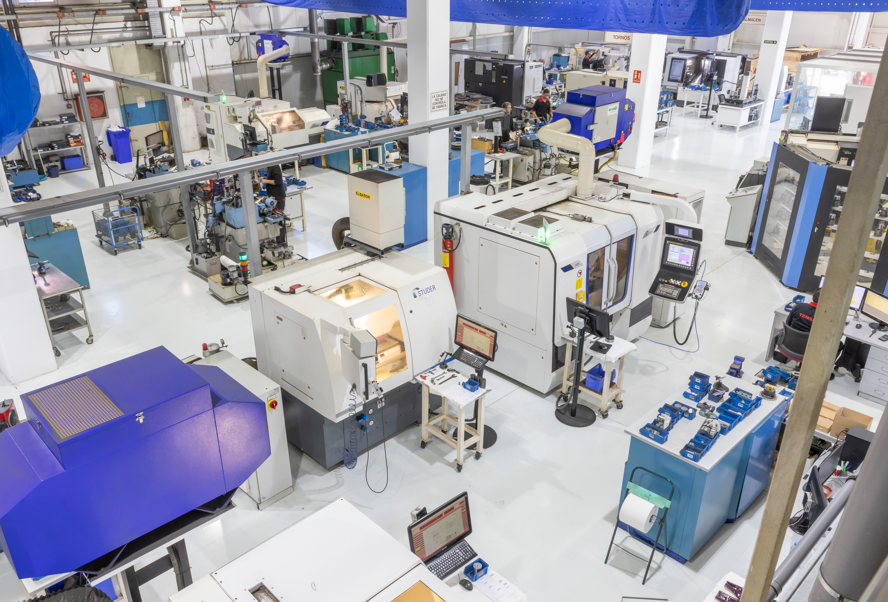
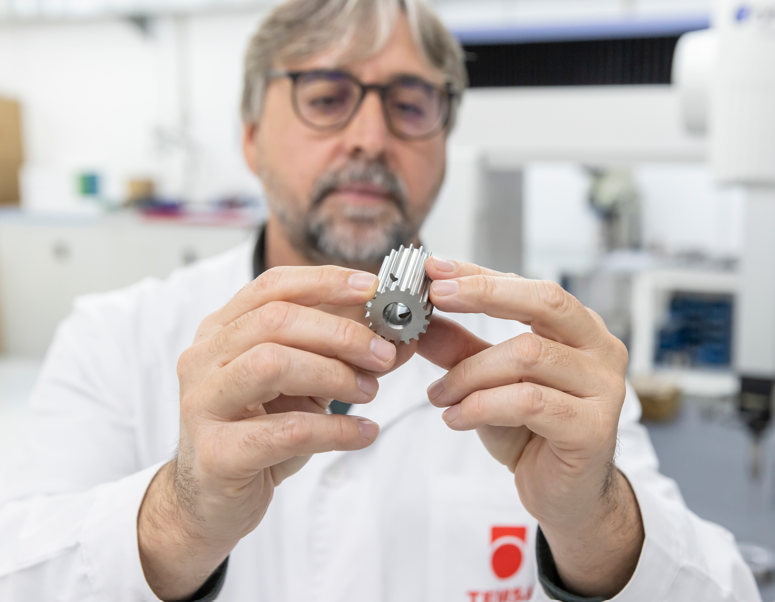
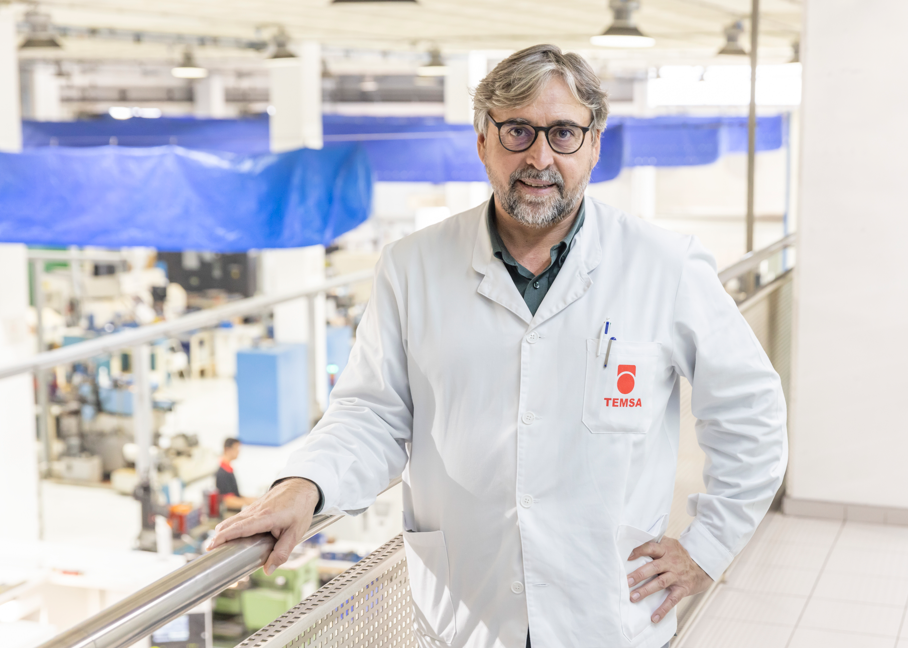
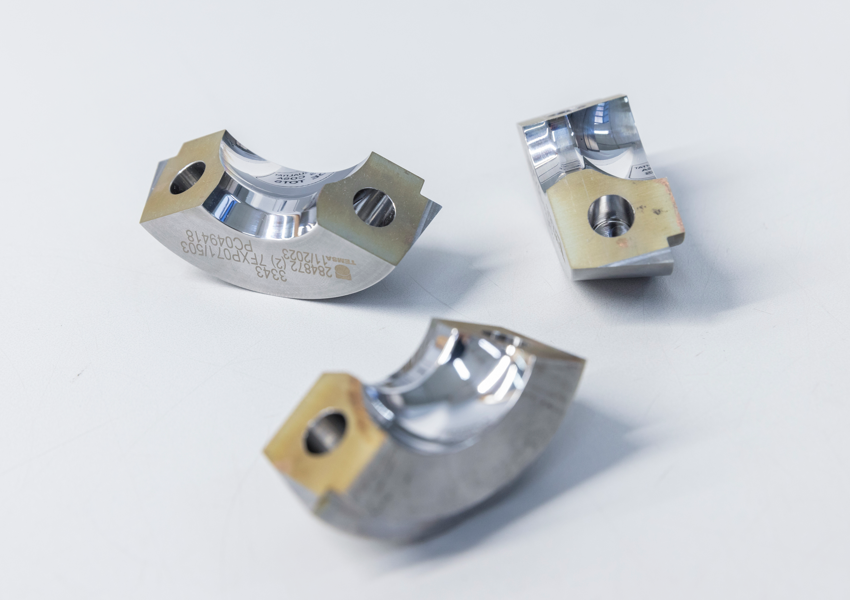
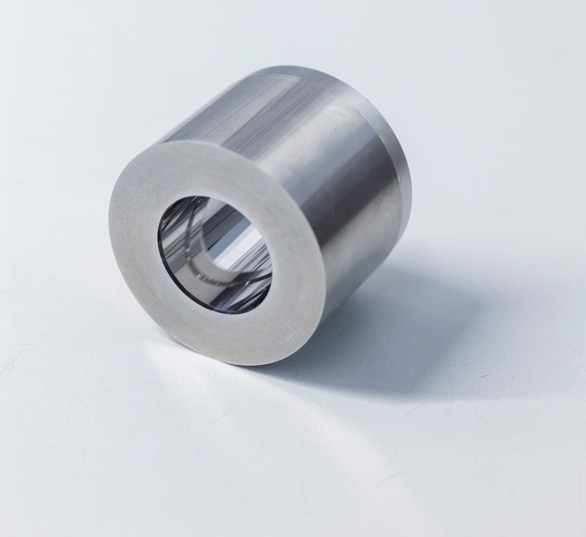
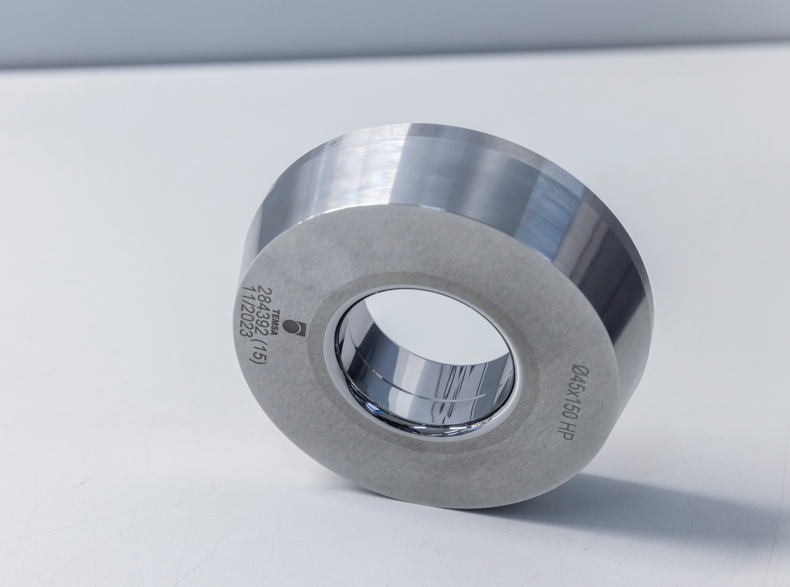